CG MATERIAL
Reaction Bonded Silicon Carbide Powder
Reaction Bonded Silicon Carbide Powder
Reaction Bonded Silicon Carbide (RBSC) Powder is a type of silicon carbide powder that is formed by a unique manufacturing process. It is made by combining a mixture of silicon carbide and carbon in a mold, which is then heated to a high temperature in the presence of a gas or vapor, causing a chemical reaction to occur.
During the reaction process, the carbon in the mixture reacts with the silicon to form silicon carbide, resulting in a dense, high-strength material with excellent mechanical properties. The resulting RBSC powder has a unique microstructure with interconnected pores, making it ideal for use in applications where high strength and thermal shock resistance are critical.
RBSC Powder is commonly used in the production of high-performance components for industrial applications, such as wear-resistant parts, furnace components, and cutting tools. It is also used in the manufacturing of electronic components and semiconductors, due to its excellent thermal conductivity and electrical properties.
RBSC Powder is available in a range of particle sizes and purity levels to meet the specific requirements of different applications. It is also available in a variety of forms, including plates, tubes, and other complex shapes, making it suitable for a wide range of manufacturing processes.
Overall, Reaction Bonded Silicon Carbide Powder is a high-performance material with unique properties that make it ideal for use in a wide range of industrial applications. Its high strength, thermal shock resistance, and unique microstructure make it an excellent choice for applications that require high-performance materials.
Silicon Carbide Ceramics Properties
Compound Formula | SiC |
Molecular Weight | 40.1 |
Appearance | Black |
Melting Point | 2,730° C (4,946° F) (decomposes) |
Density | 3.0 to 3.2 g/cm3 |
Electrical Resistivity | 1 to 4 10x Ω-m |
Poisson's Ratio | 0.15 to 0.21 |
Specific Heat | 670 to 1180 J/kg-K |
Silicon Carbide Ceramics Specification
CAS#: 409-21-2, Not Hazardous | |||
Powder, F.W. 40.10, m.p. 2700 °C, Spec. Gravity 3.217 gm/cm3 | |||
Item No. | Description | Purity | Lot Size |
CB14-85 | Silicon Carbide Powder Particle Size:18, 30, 40 or 200 mesh |
> 85 % F.C. < 2.5%, Fe2O3 < 2%, Al2O3 < 1.2% |
Customize |
CB14-90 | Silicon Carbide Powder Particle Size:18, 30, 40 or 200 mesh |
> 90 % F.C. < 1.5%, Fe2O3 < 1.2% |
Customize |
CB14-98 | Silicon Carbide Powder Particle Size:18, 30, 40 or 200 mesh |
> 98 % F.C. < 0.6%, Fe2O3 < 0.7% |
Customize |
Silicon Carbide Ceramics Applications
Until the invention of boron carbide in 1929, silicon carbide was the hardest synthetic material known. It has a Mohs hardness rating of 9, approaching that of a diamond. In addition, SiC crystal has fracture characteristics that make them extremely useful in grinding wheels and in abrasive paper and cloth products.
Its high thermal conductivity, together with its high-temperature strength, low thermal expansion, and resistance to chemical reaction and thermal shock, makes silicon carbide valuable in the manufacture of high-temperature bricks and other refractories.
SiC ceramic is also classed as a semiconductor, having an electrical conductivity between that of metals and insulating materials. This property, in combination with its thermal properties, makes SiC a promising substitute for traditional semiconductors such as silicon in high-temperature applications.
Reaction Bonded Silicon Carbide Powder Specifications
Type | SISIC-10 | SISIC-14 |
Particle Size (D50) | 7um | 10um |
SiC | > 99% | > 99% |
Fe3O2 | < 0.03% | < 0.03% |
Free C | < 0.1% | < 0.03% |
SiO2 | < 0.2% | < 0.2% |
Reaction Bonded Silicon Carbide Powder Safety Information
Safety Information according to GHS | |
Signal Word | Warning |
Hazard Statements | H315-H319-H335 |
Hazard Codes | Xi |
Risk Codes | 36/37/38 |
Safety Statements | 26-36 |
RTECS Number | VW0450000 |
Transport Information | N/A |
WGK Germany | 3 |
Reaction Bonded Silicon Carbide Powder Applications
Reaction bonded silicon carbide has proven to be an excellent material choice for wear applications such as pipe liners, flow control chokes and larger wear components in mining as well as other industries.
Packaging
We handle our products with care to ensure they remain in their original condition during storage and transportation and to preserve their quality.
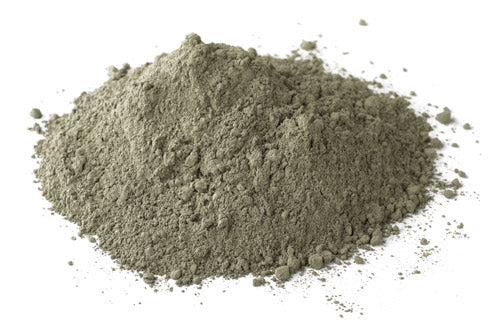