CG MATERIAL
Silicon Carbide Seats, SiC Seats
Silicon Carbide Seats, SiC Seats
Silicon Carbide (SiC) Seats are high-performance mechanical components that are commonly used in various industries for their unique properties. SiC Seats are made of silicon carbide material, which is a high-strength ceramic material that offers excellent hardness, wear resistance, and thermal shock resistance.
SiC Seats have a number of benefits over traditional seat materials like steel or bronze, including their ability to withstand extreme temperatures and pressures, their resistance to corrosion and abrasion, and their low coefficient of thermal expansion, which reduces the risk of damage to the seat due to thermal stress.
SiC Seats are commonly used in applications where high-performance seats are required, such as in pumps, valves, and other rotating machinery. They are available in a variety of shapes and sizes to fit different types of machinery, and they can be customized to meet specific application requirements.
SiC Seats are known for their high durability and long lifespan, making them a cost-effective choice for applications that require high-performance, long-lasting seats. They are also resistant to many types of chemicals, making them an ideal choice for corrosive environments.
Overall, SiC Seats are an excellent choice for applications that require high-performance, long-lasting seats that can withstand extreme conditions and provide reliable operation. They are an ideal choice for use in pumps, valves, and other rotating machinery where high durability and reliability are required.
Silicon Carbide Ceramics Properties
Compound Formula | SiC |
Molecular Weight | 40.1 |
Appearance | Black |
Melting Point | 2,730° C (4,946° F) (decomposes) |
Density | 3.0 to 3.2 g/cm3 |
Electrical Resistivity | 1 to 4 10x Ω-m |
Poisson's Ratio | 0.15 to 0.21 |
Specific Heat | 670 to 1180 J/kg-K |
Silicon Carbide Ceramics Specification
CAS#: 409-21-2, Not Hazardous | |||
Powder, F.W. 40.10, m.p. 2700 °C, Spec. Gravity 3.217 gm/cm3 | |||
Item No. | Description | Purity | Lot Size |
CB14-85 | Silicon Carbide Powder Particle Size:18, 30, 40 or 200 mesh |
> 85 % F.C. < 2.5%, Fe2O3 < 2%, Al2O3 < 1.2% |
Customize |
CB14-90 | Silicon Carbide Powder Particle Size:18, 30, 40 or 200 mesh |
> 90 % F.C. < 1.5%, Fe2O3 < 1.2% |
Customize |
CB14-98 | Silicon Carbide Powder Particle Size:18, 30, 40 or 200 mesh |
> 98 % F.C. < 0.6%, Fe2O3 < 0.7% |
Customize |
Silicon Carbide Ceramics Applications
Until the invention of boron carbide in 1929, silicon carbide was the hardest synthetic material known. It has a Mohs hardness rating of 9, approaching that of a diamond. In addition, SiC crystal has fracture characteristics that make them extremely useful in grinding wheels and in abrasive paper and cloth products.
Its high thermal conductivity, together with its high-temperature strength, low thermal expansion, and resistance to chemical reaction and thermal shock, makes silicon carbide valuable in the manufacture of high-temperature bricks and other refractories.
SiC ceramic is also classed as a semiconductor, having an electrical conductivity between that of metals and insulating materials. This property, in combination with its thermal properties, makes SiC a promising substitute for traditional semiconductors such as silicon in high-temperature applications.
Silicon Carbide Seat Specifications
Type |
Material |
Description |
Sintered Silicon Carbide (S-SiC) |
Basic pure SiC |
Purity of SiC > 98% Hv: 26 GPa |
Graphite impregnated |
15%~20% content of Graphite |
|
Porous |
Better friction resistance |
|
Reaction Bonded Silicon Carbide (RB-SiC) |
Basic SiC |
Purity of SiC > 88% |
Graphite impregnated |
20%~30% content of Graphite |
Silicon Carbide Seat Applications
-Silicon carbide can be applied in areas such as semiconductor and coating.
-Silicon carbide is an ideal material for pump gaskets.
Packaging
We handle our products with care to ensure they remain in their original condition during storage and transportation and to preserve their quality.
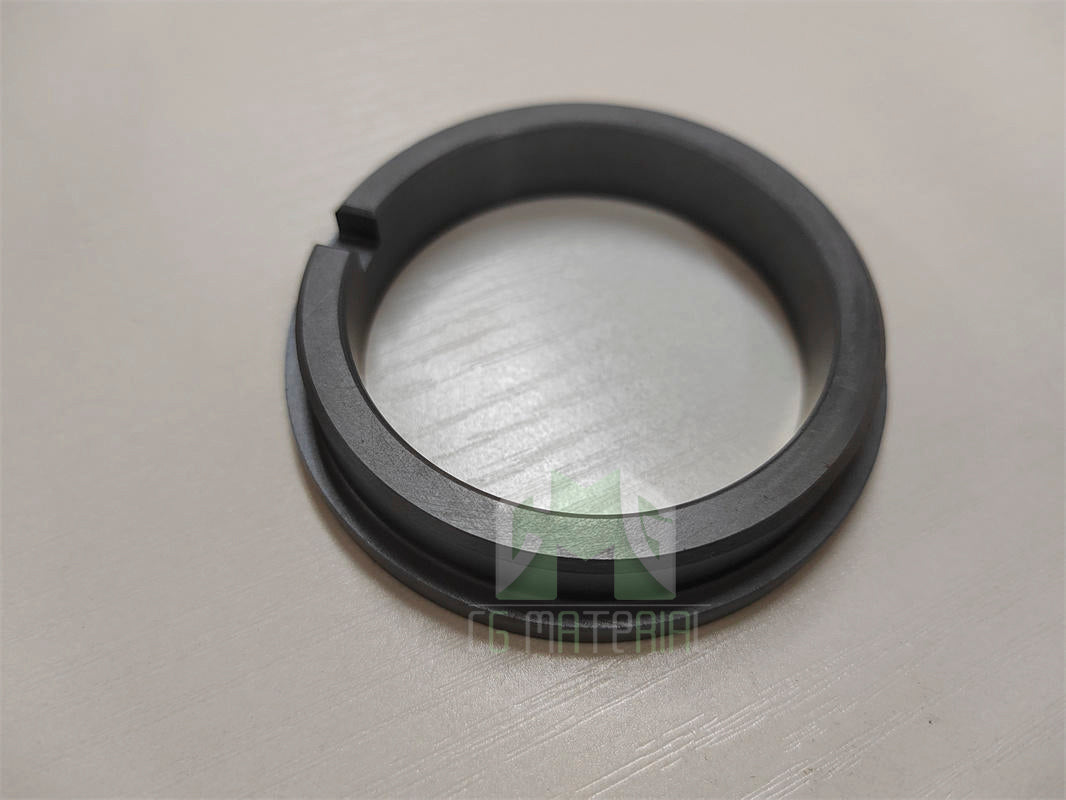
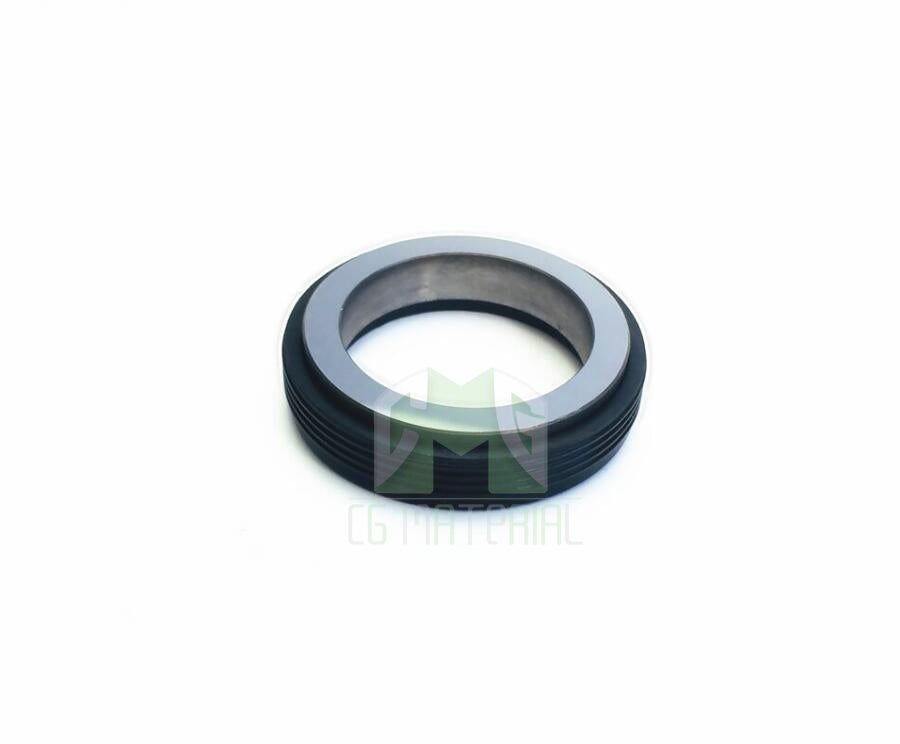